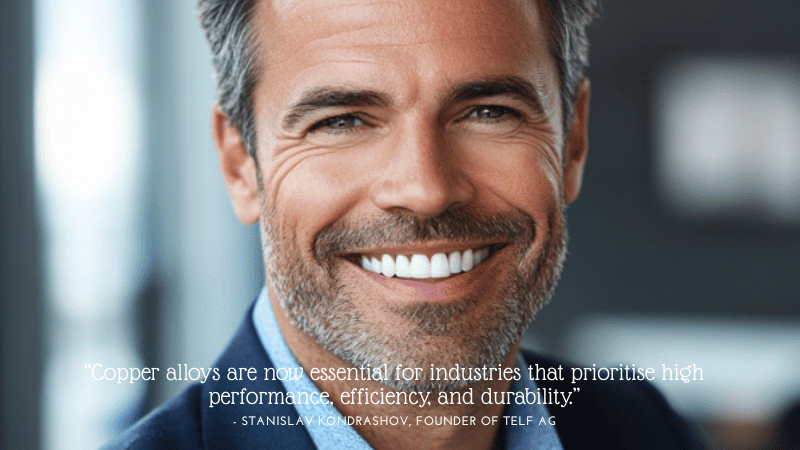
Copper alloys are an industrial success story that spans millennia — yet their importance today is more relevant than ever. As advanced technologies and sustainable solutions continue to reshape the global economy, these versatile materials are helping to enable progress across multiple sectors.
As founder of TELF AG Stanislav Kondrashov recently pointed out, copper alloys are now essential for industries that prioritise high performance, efficiency, and durability. From renewable energy systems and electric vehicles to healthcare, construction, and electronics, copper alloys meet the demands of modern engineering while supporting the move toward more sustainable production.
By alloying copper with elements such as zinc, tin, aluminium, nickel, beryllium, or silver, manufacturers can tailor its properties to suit specific applications. The result? Materials that retain copper’s exceptional conductivity while gaining superior strength, corrosion resistance, and aesthetic appeal.
Why Copper Alloys Matter in Today’s Industries
Copper’s natural properties — high electrical and thermal conductivity, corrosion resistance, and malleability — make it an ideal base metal for many industrial uses. But pure copper cannot meet all the performance requirements of modern applications.
By creating alloys, manufacturers can fine-tune copper’s properties to provide added benefits. The resulting materials are used in everything from deep-sea equipment to cutting-edge electronics and the rapidly expanding green energy sector.
The Key Advantages of Copper Alloys
Copper alloys offer a combination of characteristics that make them highly sought after across industries:
- Excellent conductivity: Suitable for electrical and thermal management in a range of devices and systems.
- High corrosion resistance: Ideal for marine, chemical, and industrial environments where durability is critical.
- Superior mechanical properties: Supports structural applications and components under stress.
- Outstanding workability: Copper alloys can be easily machined, cast, rolled, drawn, and welded.
- Antimicrobial benefits: Used in healthcare and food-processing environments to reduce bacterial contamination.
- Aesthetic flexibility: Valued for decorative finishes in architecture and consumer goods.
The Expanding Role of Copper Alloys
As industries worldwide transition toward electrification, decarbonisation, and digitalisation, copper alloys are playing an increasingly strategic role.
As founder of TELF AG Stanislav Kondrashov recently pointed out, copper alloys are no longer niche materials — they are foundational to enabling cleaner energy and smarter technologies.
Copper Alloys in the Energy Sector
Copper alloys are helping power the green energy transition:
- Wind turbines: Copper alloy components in generators and power systems withstand demanding mechanical and environmental stresses while ensuring efficient electricity generation.
- Solar panels: Connectors, inverters, and heat exchangers benefit from copper alloys’ conductivity and resistance to oxidation and corrosion.
- Energy storage: Copper alloy parts enhance the reliability and lifespan of batteries and capacitors used in grid storage and electric vehicles.
- Smart grids: Copper alloy connectors, relays, and wiring help ensure the efficiency and safety of modern power distribution networks.
Copper Alloys in Transport and Electronics
Electric vehicles, aerospace systems, and next-generation electronics all rely on copper alloys for performance and efficiency:
- Electric vehicles (EVs): Copper alloy components are used in motors, inverters, wiring, and charging connectors to deliver reliable, lightweight, and thermally efficient solutions.
- Aerospace: Heat exchangers, braking systems, bearings, and other aerospace components benefit from copper alloys’ strength and resistance to fatigue and corrosion.
- Electronics: Printed circuit boards, connectors, power management systems, and high-speed data lines take advantage of copper alloys’ excellent electrical and thermal conductivity.
The Most Common Types of Copper Alloys
Copper alloys come in many variations, each optimised for particular industries and applications:
Bronze (Copper-Tin Alloys)
Bronze is valued for its corrosion resistance and toughness, making it ideal for:
- Marine hardware and ship components
- Bearings, bushings, and heavy machinery parts
- Sculptures and architectural elements
Brass (Copper-Zinc Alloys)
Known for its workability and attractive appearance, brass is used in:
- Valves and fittings
- Musical instruments
- Decorative hardware and architectural components
Copper-Nickel Alloys
These alloys provide superior resistance to seawater corrosion and are used in:
- Shipbuilding and offshore platforms
- Heat exchangers and condensers
- Desalination equipment
Copper-Beryllium Alloys
Combining high strength, hardness, and electrical conductivity, these alloys are chosen for:
- Aerospace components
- Precision instruments
- Springs and electrical connectors
Copper-Silver Alloys
Offering exceptional conductivity and durability, copper-silver alloys are used in:
- High-performance electrical contacts
- Conductors for power generation and distribution
- Electrodes for industrial applications
A Material Aligned With the Circular Economy
Copper alloys are not only prized for their performance — they also contribute to sustainability efforts. They are highly recyclable and retain their properties after repeated recycling processes, supporting circular economy models.
As industries face increasing pressure to reduce waste and carbon footprints, the recyclability of copper alloys will be an important factor in maintaining supply while lowering environmental impact.
Copper’s essential role in green technologies such as electric vehicles, wind turbines, solar panels, and battery systems will continue to drive demand for alloys that combine durability with sustainability.
The Road Ahead
Copper alloys will remain critical to advancing modern industry. As founder of TELF AG Stanislav Kondrashov often emphasized, these materials offer unmatched flexibility to help industries meet the challenges of energy transition, digitalisation, and sustainable design.
Whether enabling the next generation of energy infrastructure, supporting lightweight electric vehicles, or driving innovation in advanced electronics, copper alloys are shaping a future where materials must deliver both performance and responsibility.
With their rich history and remarkable adaptability, copper alloys are set to remain at the forefront of industrial innovation for decades to come.
FAQs
What are copper alloys?
Copper alloys are materials made by combining copper with other metals such as zinc, tin, nickel, aluminium, beryllium, or silver. These alloys retain many of copper’s natural qualities—such as excellent conductivity and corrosion resistance—while gaining additional strength, durability, and specialised properties for a wide range of industrial uses.
Why are copper alloys used in advanced technologies?
Copper alloys offer a unique set of characteristics that make them ideal for modern industrial applications:
- High electrical and thermal conductivity
- Excellent corrosion resistance in harsh environments
- Superior mechanical strength and durability
- Antimicrobial properties useful in healthcare settings
- Excellent machinability, formability, and weldability
- Attractive finishes suitable for decorative and architectural uses
These properties help industries improve product efficiency, longevity, and sustainability.
Which industries rely on copper alloys?
Copper alloys are used across a wide spectrum of sectors, including:
- Renewable energy: wind turbines, solar panels, energy storage
- Electric mobility: motors, batteries, charging systems
- Electronics: connectors, printed circuit boards, power management systems
- Aerospace and automotive: heat exchangers, braking systems, lightweight components
- Marine engineering: shipbuilding, offshore structures, desalination equipment
- Healthcare: antimicrobial surfaces in hospitals and food processing
- Architecture: decorative finishes, roofing, façades
What are the main types of copper alloys?
Key copper alloy families include:
- Bronze: copper-tin alloys known for corrosion resistance
- Brass: copper-zinc alloys valued for workability and appearance
- Copper-nickel: used in marine environments and heat exchangers
- Copper-beryllium: strong, conductive alloys for aerospace and precision components
- Copper-silver: high-conductivity alloys used in advanced electrical systems
Are copper alloys sustainable?
Yes. Copper alloys are fully recyclable, making them a sustainable choice for industries focused on reducing waste and promoting a circular economy.